Products
OUR PRODUCT RANGE
Surface Preparation System
SFS Innovative Solutions Provides Dip Chemical Treatment with PLC Based Transportation or Electrically
operated Over Head Hoist for Material Movement.
Pre-Treatment are designed to improve processing quality and to conserve energy. high-performance washing system (Parallel Separator), and counter-flow circulation tank in the degrease process, and high-pressure spray water washing processes.
Accessories:
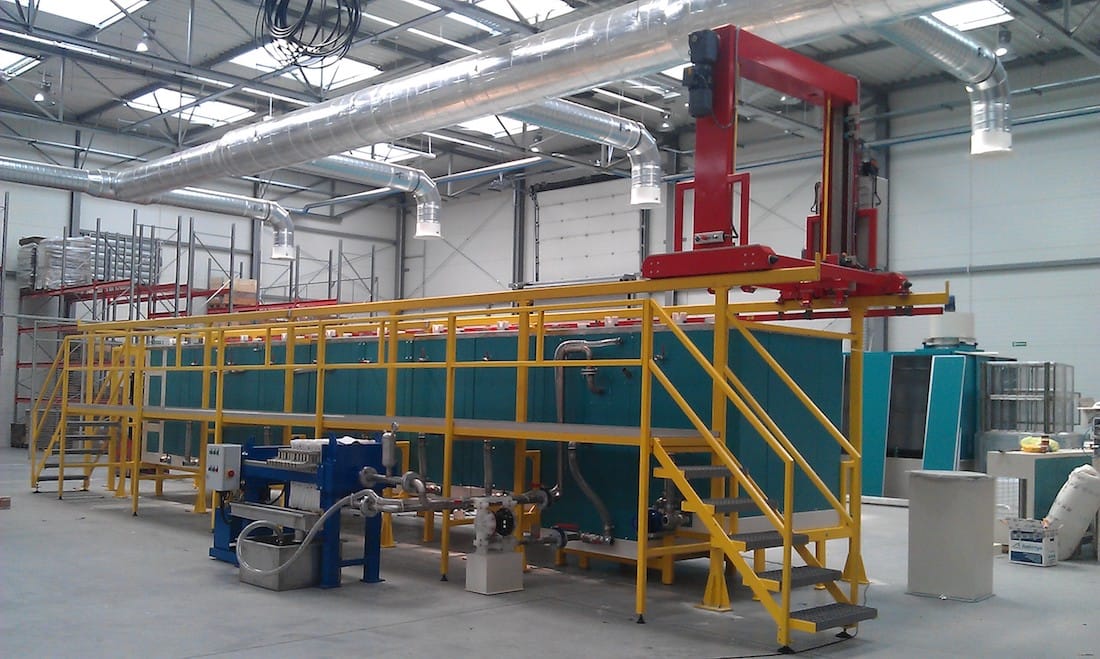
- PHE
- Sludge Separator System
- Oil skimmer System
- Auto Dosing System
- Water Treatment System
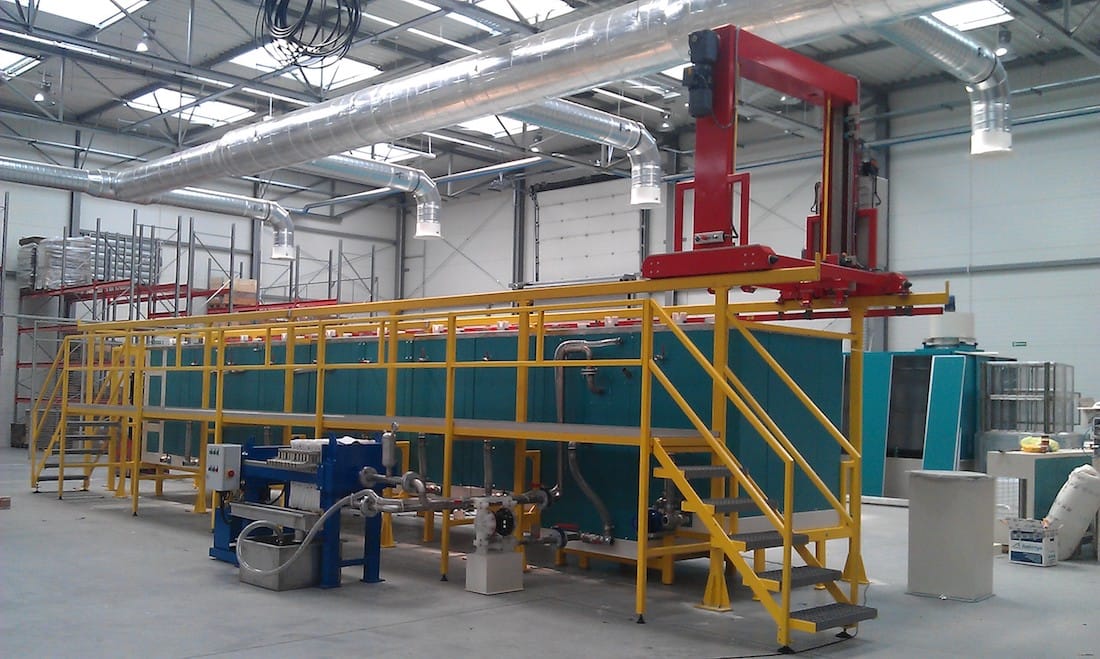
SFS Innovative Solutions PT Lines are used for large painting lines and automotive components, it gives fully
automatic operations for online surface pre-treatment and also gives excellent and uniform results.
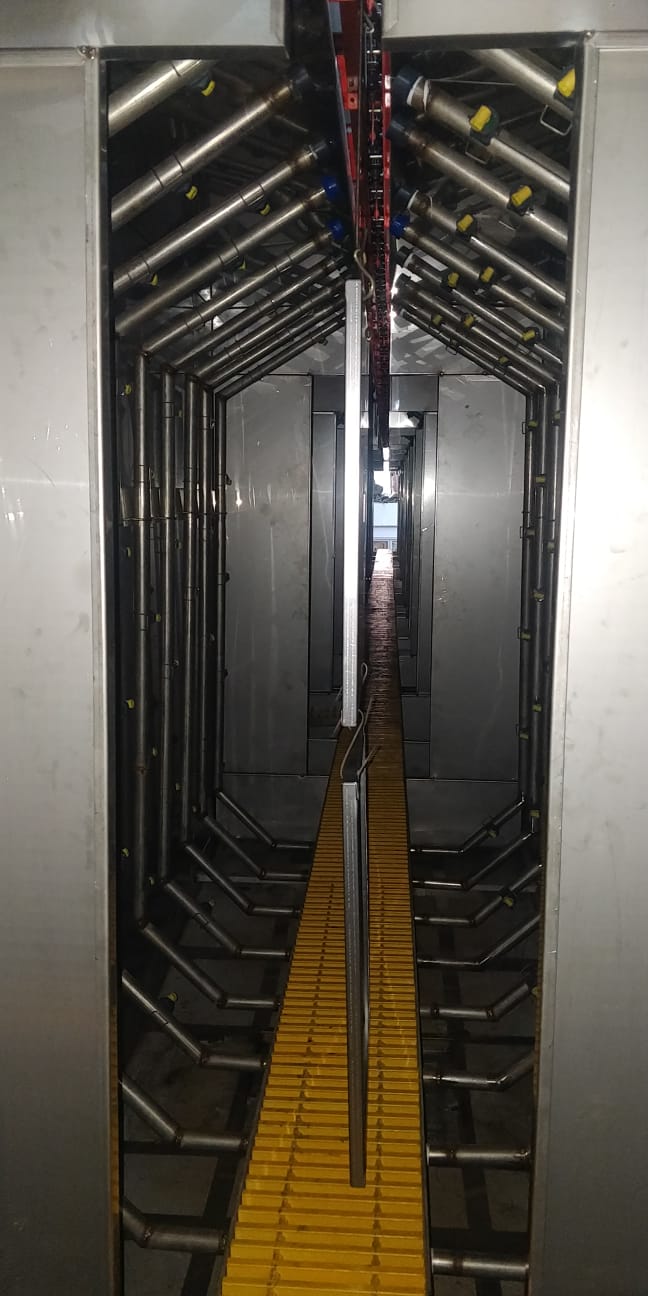
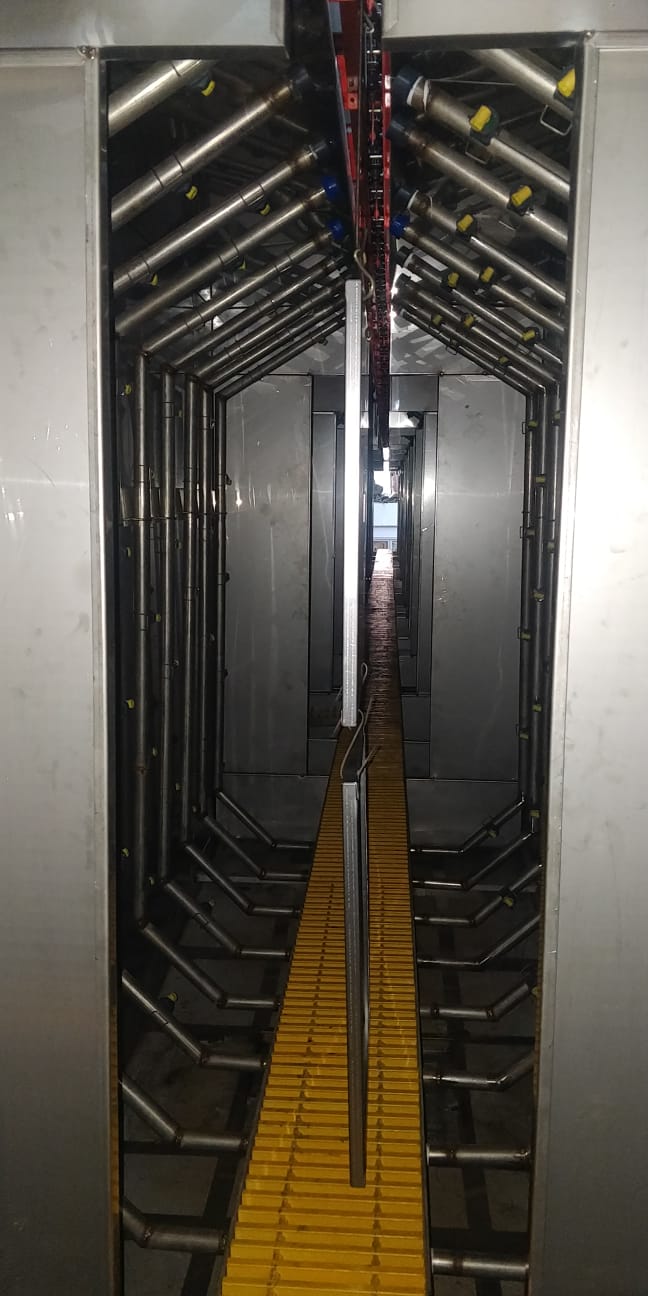
CED Plant System
Cathode Electro Deposition is most advanced and enviroment friendly Water Based coating to be done on metal components. A combination of dip and spray ensures reach of paint at every corner of component having intrinsic shape as well. CED process is industrially used for applying coatings to metal fabricated products. It has been widely used to coat automobile bodies and parts, tractors and heavy equipment, electrical switch gear, appliances, metal furniture, beverage containers, fasteners, and many other industrial products.
In short ED method is one of the most efficient methods for primer coating suitable for large volume production for coating complex form items, or where high corrosion resistant coating is required. Paint material utilisation is approaching 95 to 99%. Corrosion resistance measured in salt spray is excellent and no other painting method can compete with ED method in primer coating. For all these reasons ED painting is indispensable technology which all industrialized countries must master. On the other hand ED painting requires more technically competent operators than other painting methods do and it is sometime seen that a whole investment of ED painting line is abandoned after a trouble infested operation continued many months unsuccessfully and finally the owner changes to other methods. CED is chemically resistant, mechanically durable, pleasant in appearance having very Good Salt Spray life and is sought for by all automobile users.
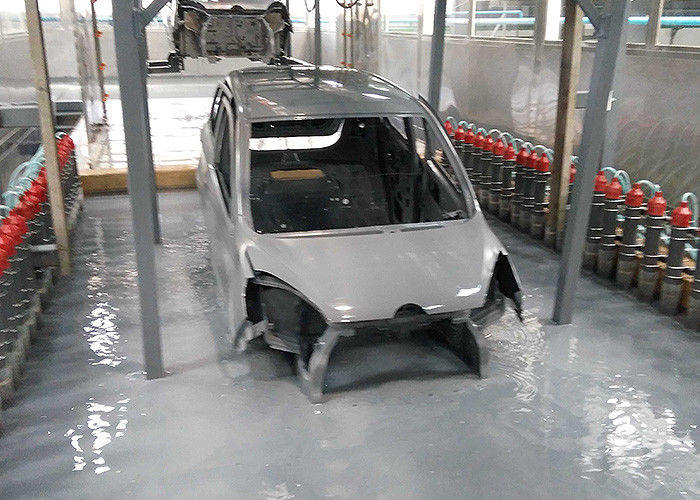
- Fully automatic operation, Film thickness can be controlled.
- Uniform coating.
- Better coverage in box and interior surfaces.
- Good coverage of sharp corners.
- No runs and sags.
- No solvent boils.
- Better chip and corrosion resistance.
- Nearly 100% paint utilization.
- Superior in anti-pollution, safety, health hazards.
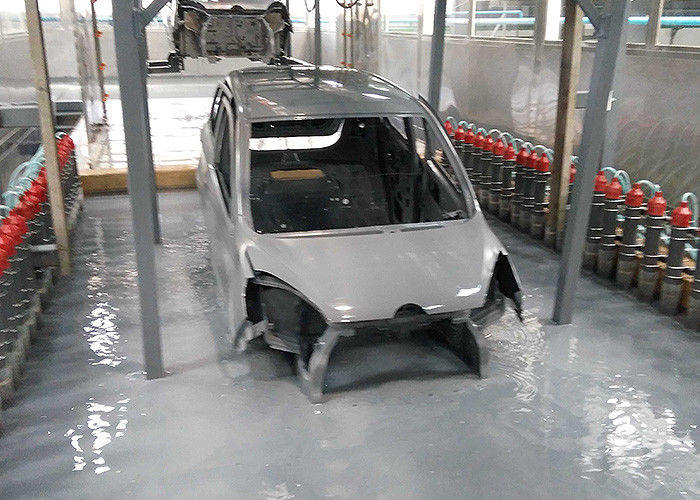
Liquid Painting System
In Paint shops paint booth is the most important area, the paint application on objects/products is done here, combined with ASU it almost consume half of the power of the overall paint shop. SFS provides booths with advanced energy savings techniques.
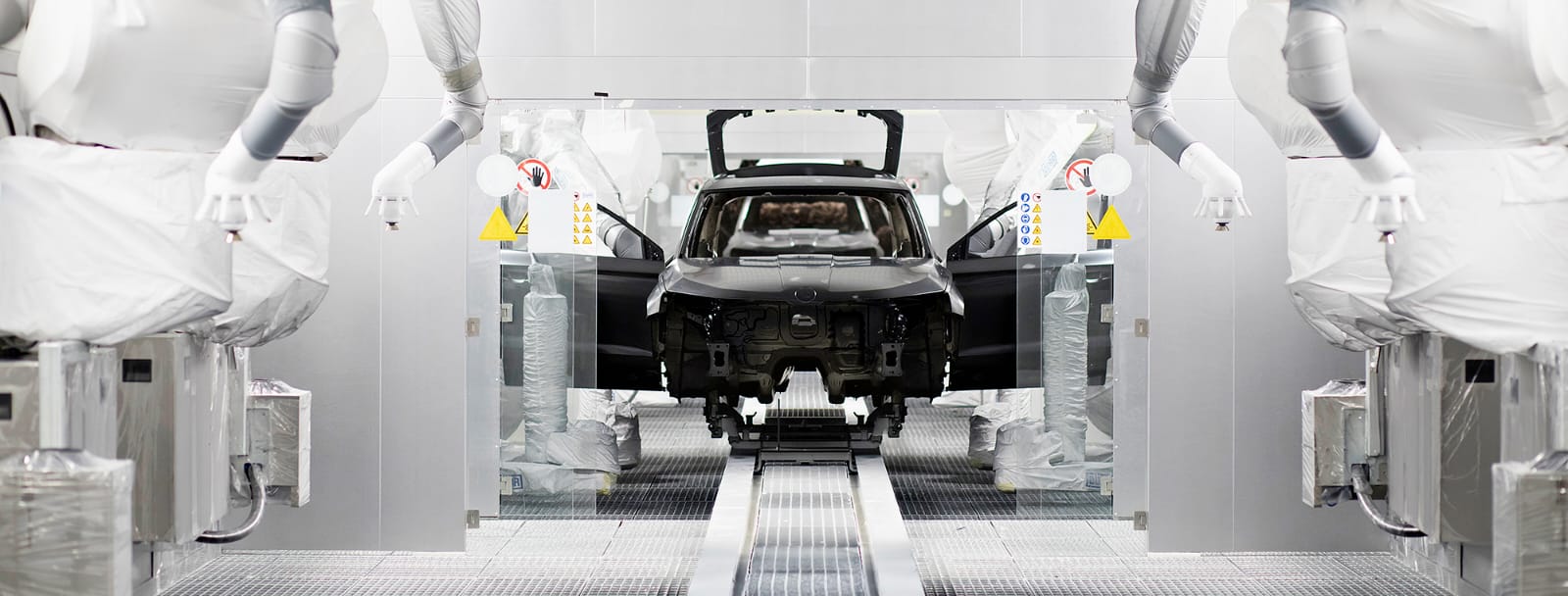
- Wet Booths – Circulation of water is provided in these booths to remove excess paints and solvents wet booths are used for mass production.
- Wet booths are of Two types
- Side draft Booth
- Down draft Booth
- Dry Booths – With paint arrestor filters in exhaust these booths are used for touch up/correction work.
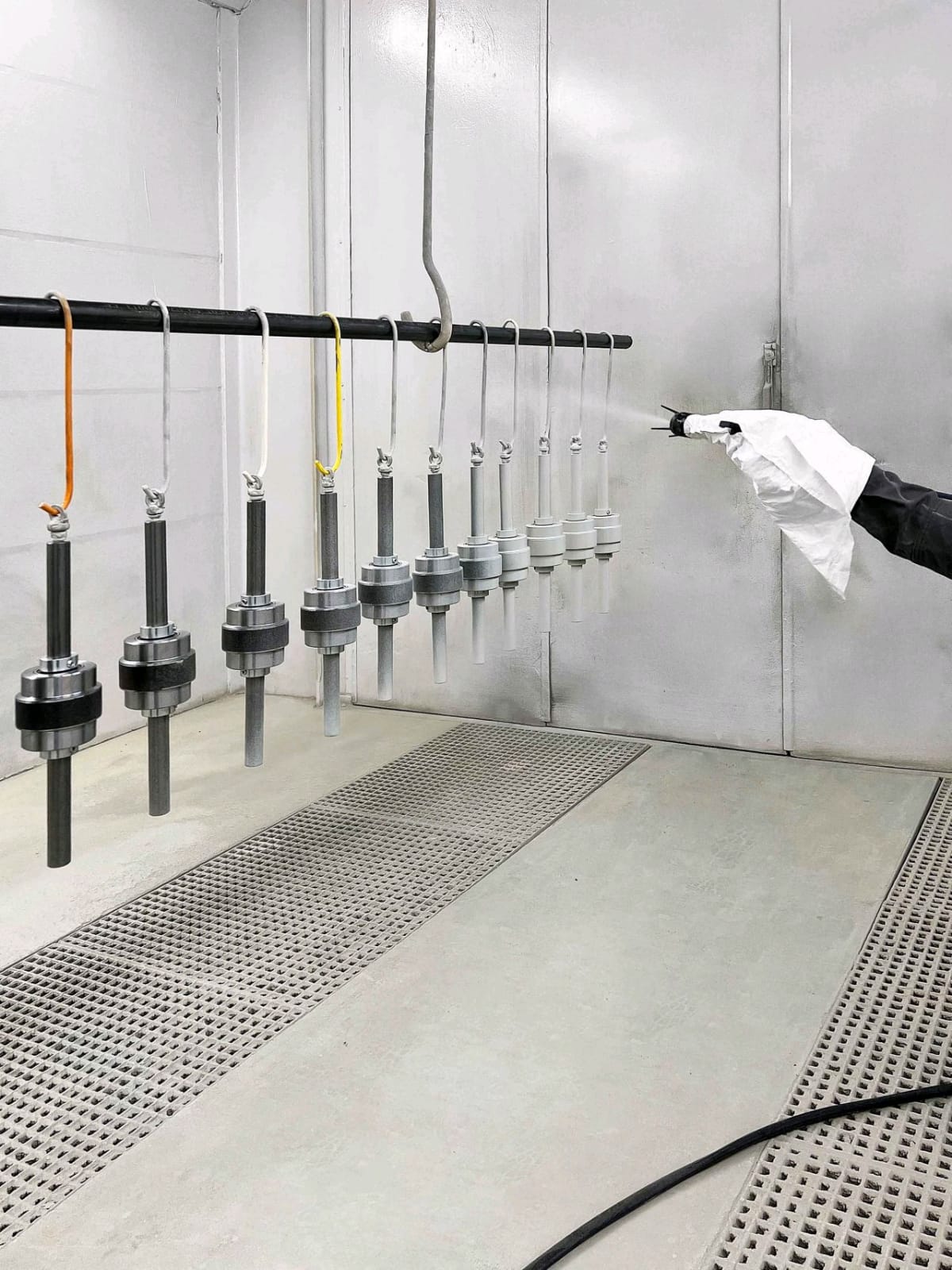
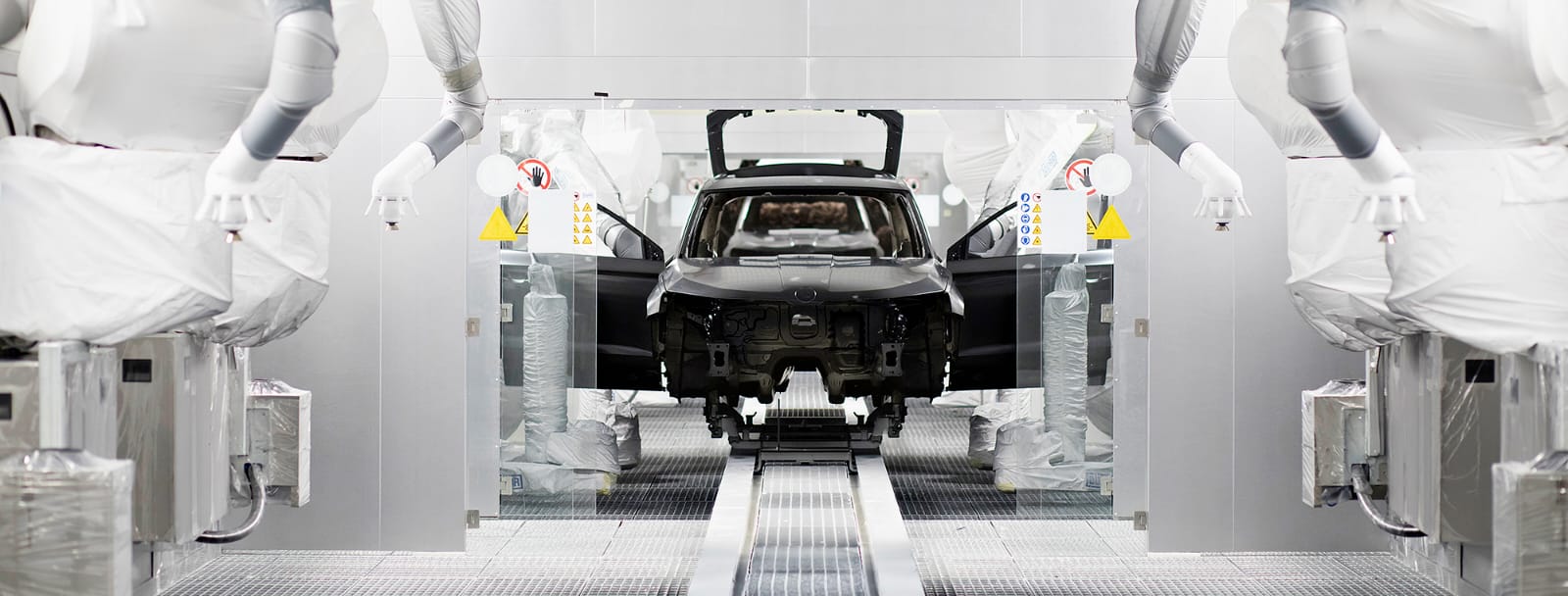
Powder Coating System
Powder Coating is an advanced environment friendly painting method,
which obtains paint film by putting powder paints to an object to be painted
and by melting with the use of Powder Curing Oven. It is the most exciting
finishing method introduced in past 100 years. Powder Coating offers
significant performance advantages with reduced costs. It also meets
environment regulations.(No VOC emission, no paint sludge disposal).
The Powder Coating Plant configuration depends upon sizes and
shapes of the articles, coating quality required in conjunction with the color
change intervals. Our specialists in surface coatings have individual answers
and concepts for all these requirements.
Conveyorised powder coating plants are specially designed suitable for
powder coating of high volumes, small & large sizes of components. The
conveyorised applications give better and uniform coating qualities with
better process controls. These plants can be supplied with automated
painting guns and reciprocators etc.
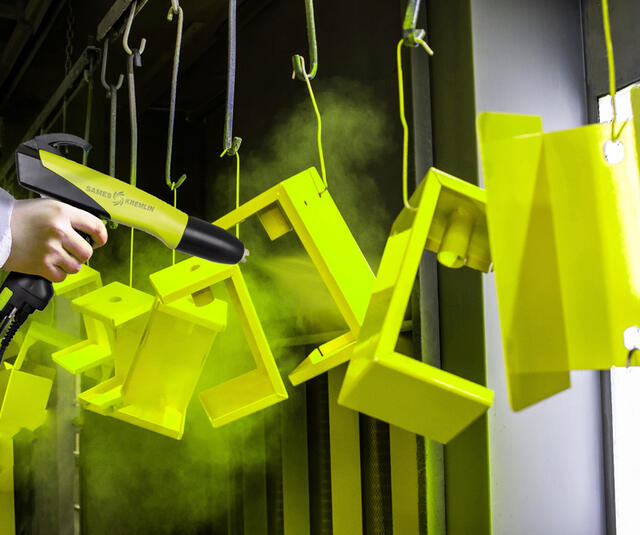
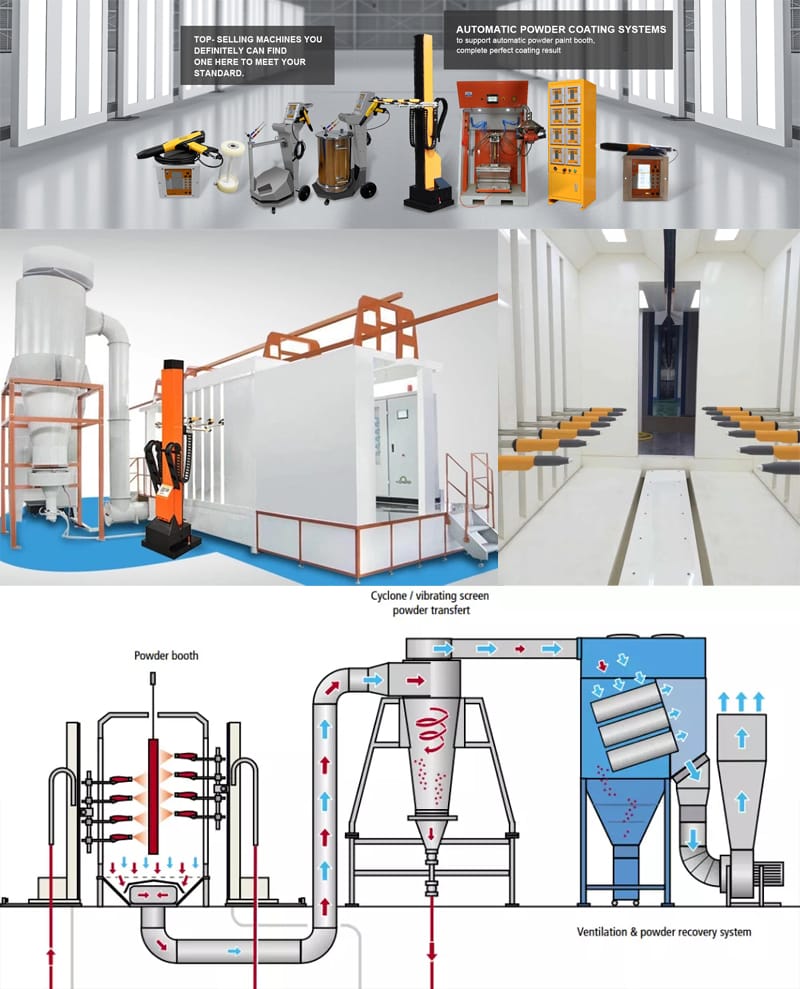
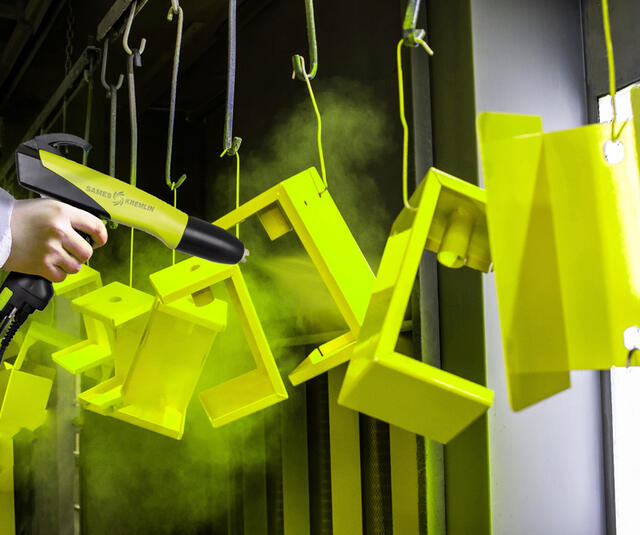
Curving Ovens
Ovens are designed to consume low power/Fuel with a uniform temperature throughout the Oven. Various
safety features like Blower/Heat Source interlock, Pressure release mechanisms and Auto Shut-offs are
provided to make these ovens fully safe. ovens can be heated by:
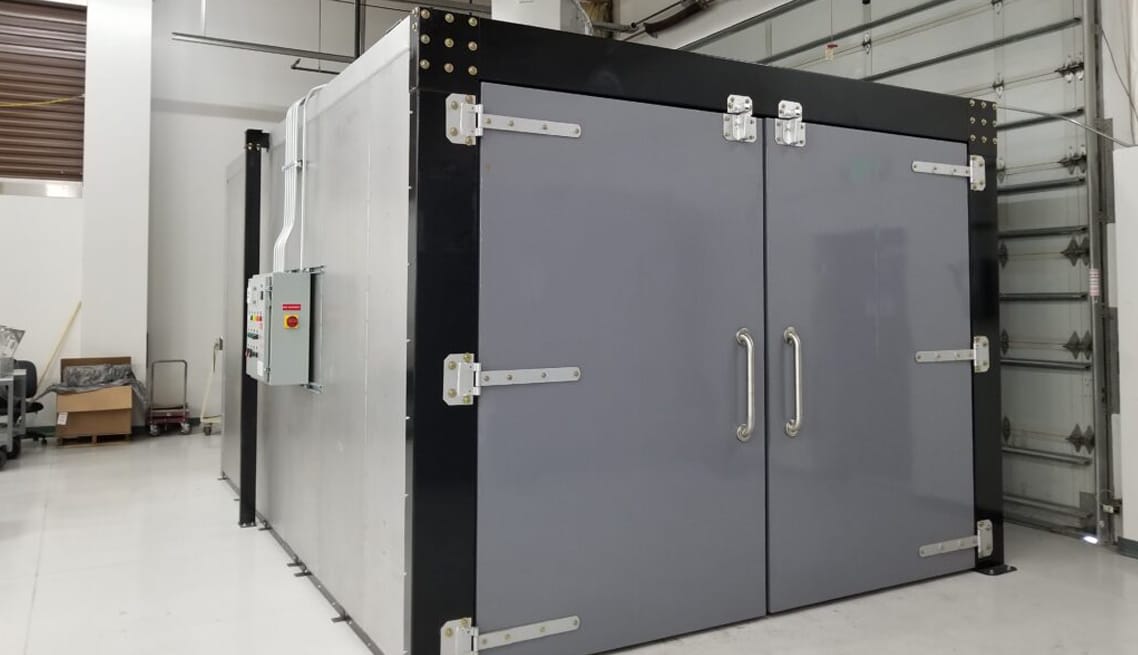
- Electric Heaters Normally for Small Batch Type Applications.
- Gas Fired- CNG / PNG/ LPG /Propane-Normally used for large ovens . The Gas fired ovens can be – Direct Fired – In-Direct Fired.
- IR Heated-normally used for Plastic/ABS curing in a Tunnel type Oven.
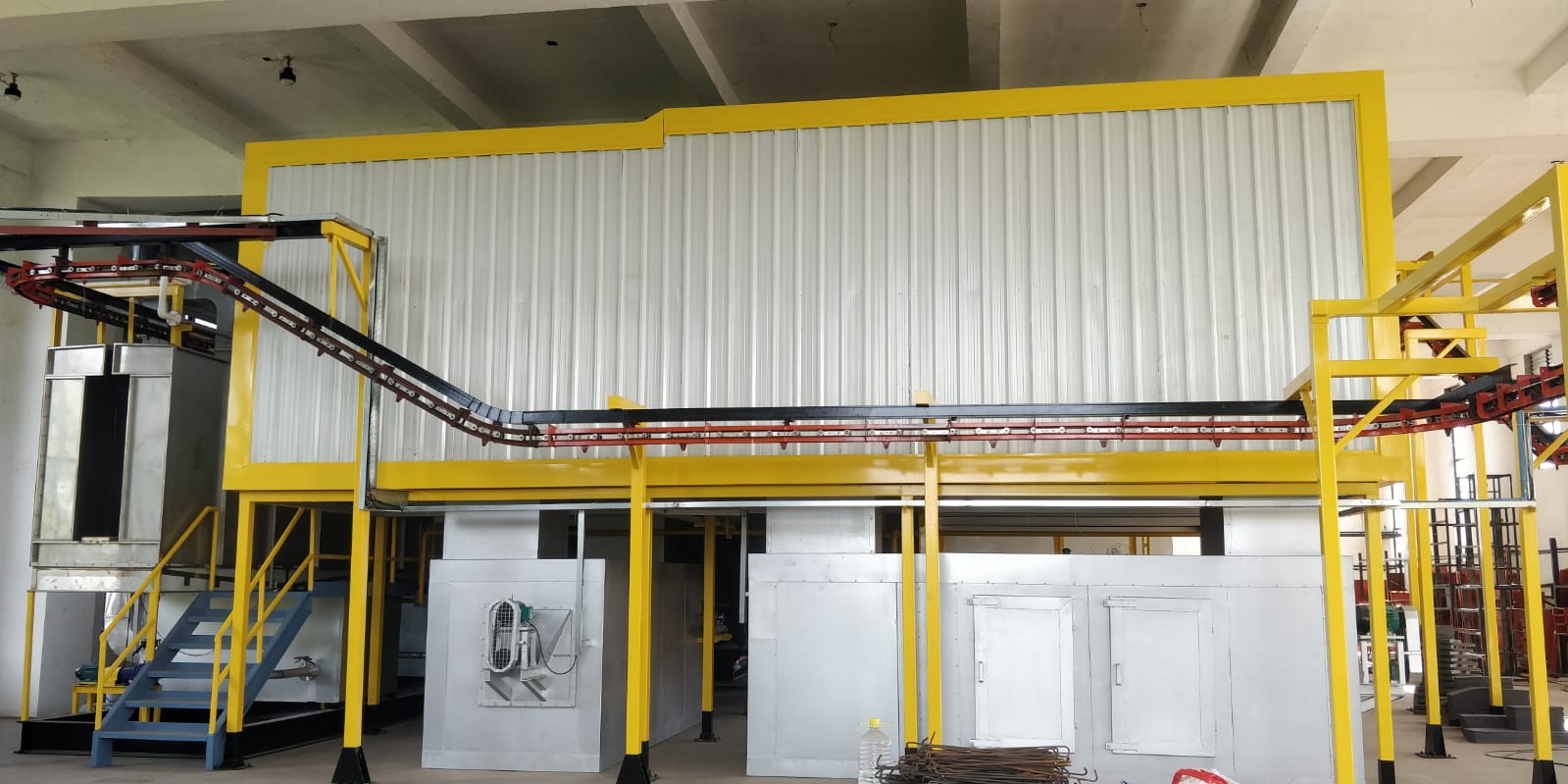
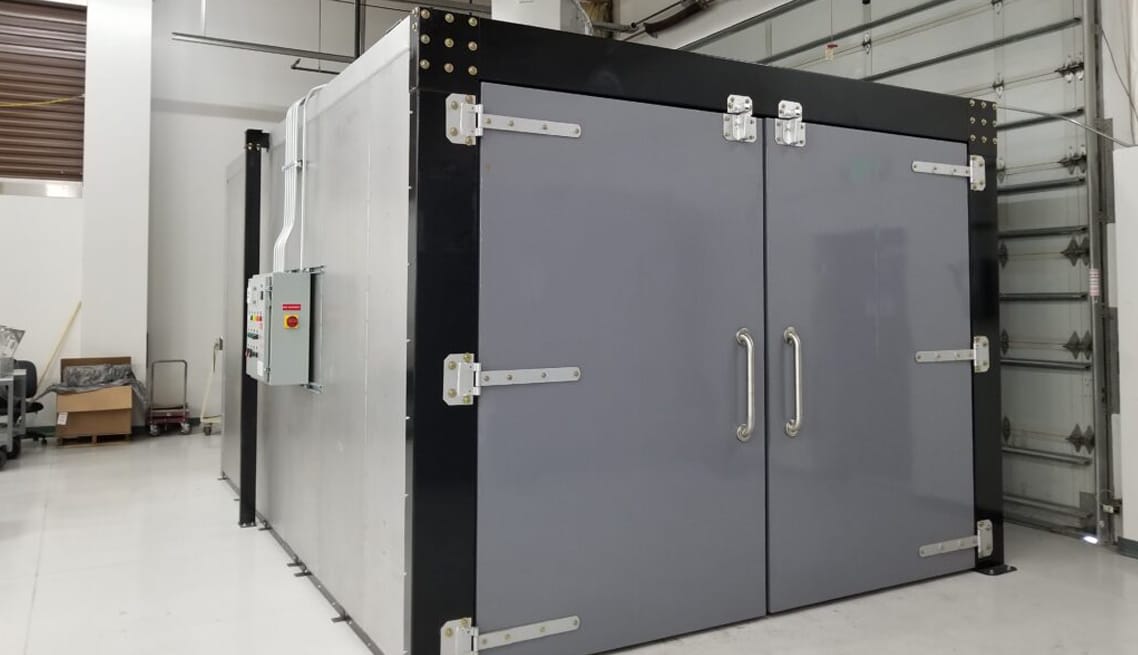
Electric Control Panels
The Control panels are very critical in
Paint Shops and Blasting Machine. The
operations, efficiency, safety of the plant
depends on the control panel design. SFS
Innovative Solutions provides following
types of Control Panels.
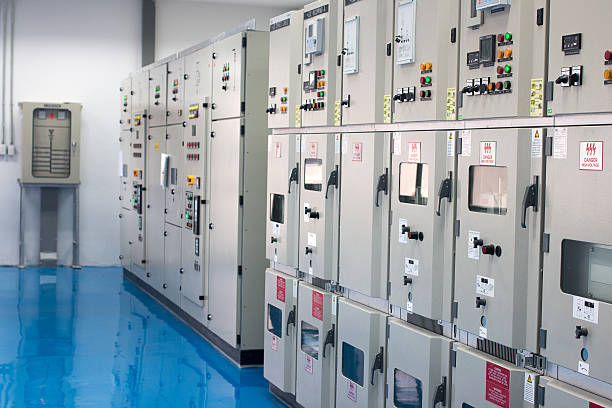
- Conventional type of panels
- PLC/Touchscreen Panels
- Scada Based Control Panels
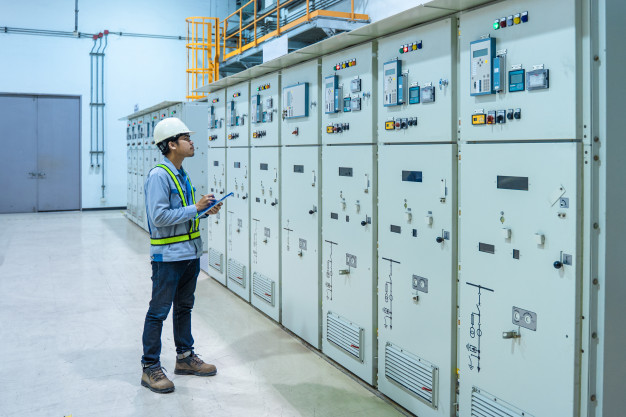
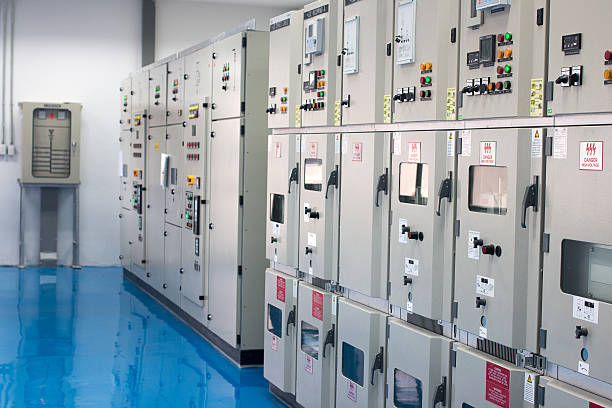
Shot-Blasting
Shot-Blasting is a method used to clean,
strengthen (peen) or polish metal. Shot
blasting is used in almost every industry that
uses metal, including aerospace, automotive,
construction, foundry, shipbuilding, rail, and
many others. There are two technologies
used: Wheel Blasting or Air blasting. It helps in
reducing the water pollution considerably.
Wheel-Blasting directly converts electric
motor energy into kinetic abrasive energy by
rotating a turbine wheel.
Air Blast machines can take the form of
a blast cabinet, the blast media is
pneumatically accelerated by compressed air
and projected by nozzles onto the
component.
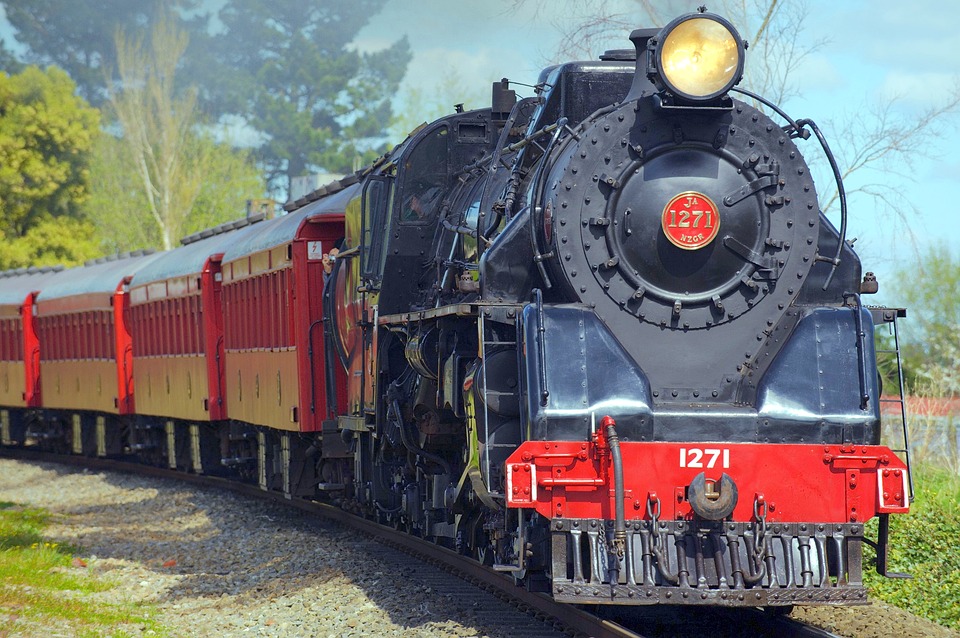
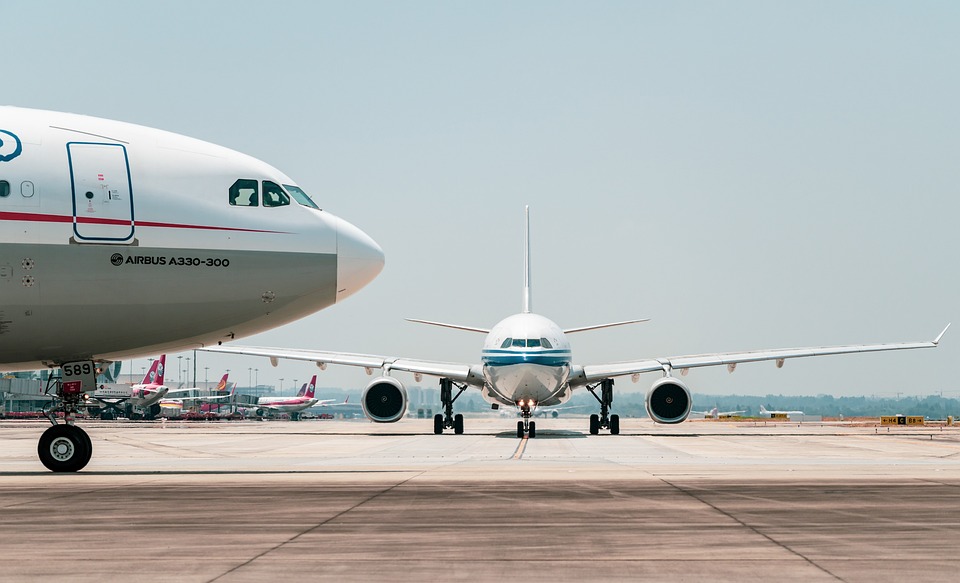
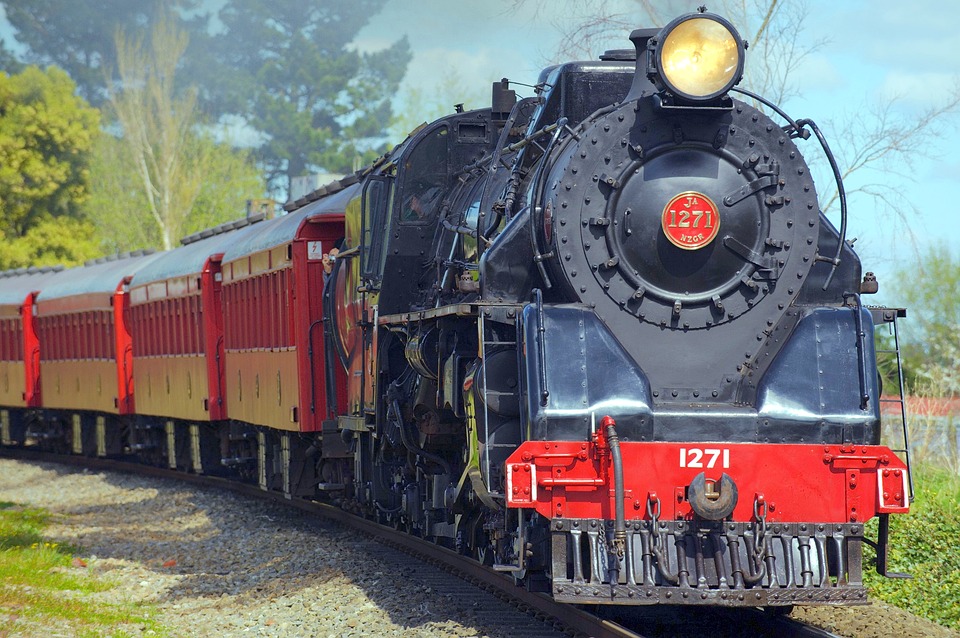
Types of Shot Blasting Machine
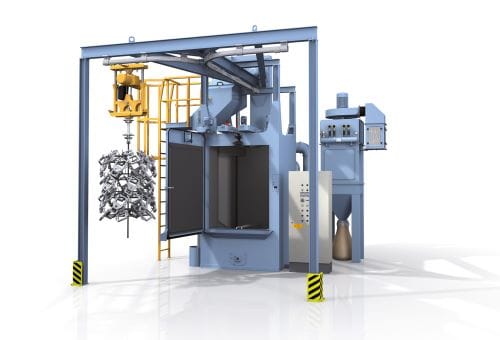
- Air Operated Shot Blasting Machine -Portable Blasting Machine. – Cabinet Type Shot Blast Machine.
- Airless Shot Blasting Machine – Tumblast Type Shot Blasting Machine. – Table Type Shot Blasting Machine. – Hanger Type Shot Blasting Machine. – Diabola Tunnel Type Shot Blasting Machine. – Belt Conveyor Type Shot Blasting Machine. – Roller Conveyor Type Shot Blasting Machine. – Coil & Wire Shot Blasting Machine. – Shot Peening Machine.
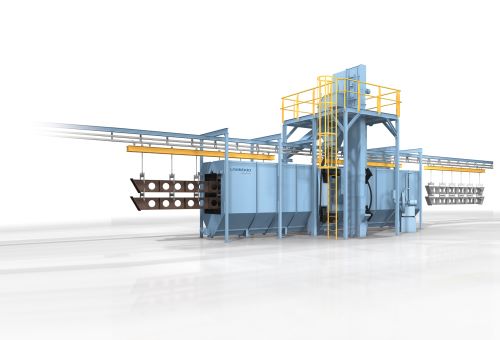
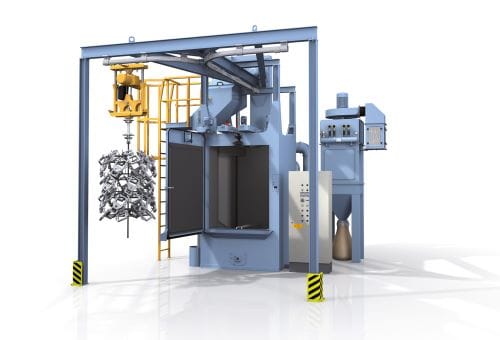
Blast Room Systems
The main feature of blast room system is that the operator is inside the room during the blasting process. A
protective suit and a helmet protect the operator from abrasive impact, and a fresh air supply provides sufficient
ventilation through the blaster’s helmet.
Blast rooms are used for big components or components where automatic blasting would be too expensive. In
combination with nozzle manipulators installed in the blast room, surfaces can be automatically processed and
areas that are hard to access can be blasted manually. Thus, the flexibility is maintained whilst reducing the number
of blasters needed.
Blast Room System Includes Following Features:
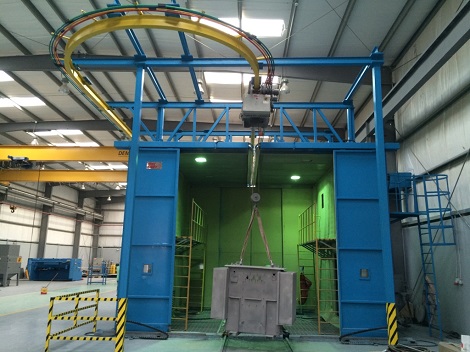
- Abrasive Blasting Machine.
- Abrasive Recovery & Re-cycling System.
- Dust Collectors
- Job Handling System.
- Wall Protection Rubber Lining.
- Illumination.
- Electric Control Panel.
- Operator Safety Wears.
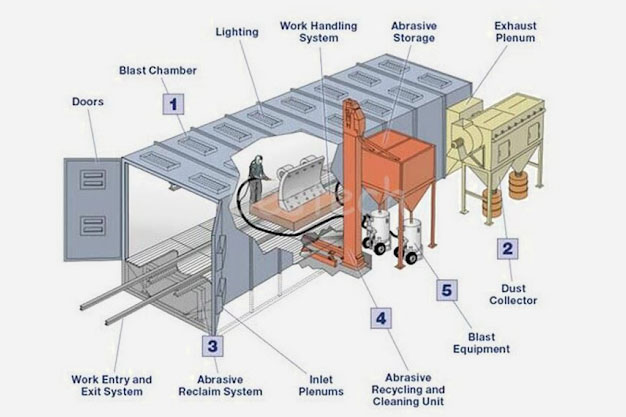
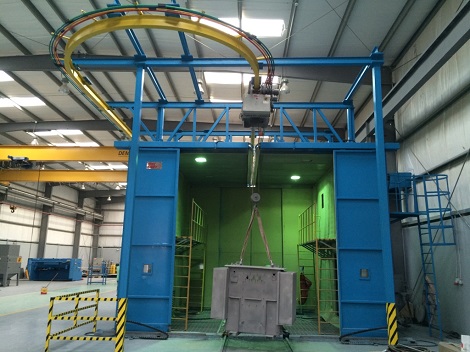
Liquid & Powder Coating Equipment
At SFS, we utilize our technical expertise and experience to deliver turnkey paint finishing systems that ensure highest levels of production efficiency, operating flexibility and superior performance, while offering our customers an unlimited range of coating options.
Our application systems have been enhanced with Intelligent Control system for high volume paint production line and further a remarkable increase in paint shop efficiency.

- Automatic Spray Guns – Conventional / HVLP / Electrostatic.
- High Speed Rotary Atomisers (Bells) / Liquid and Powder.
- Reciprocating systems(Liquid and Powder)
- 1k, 2k and 3k Paint Circulation System
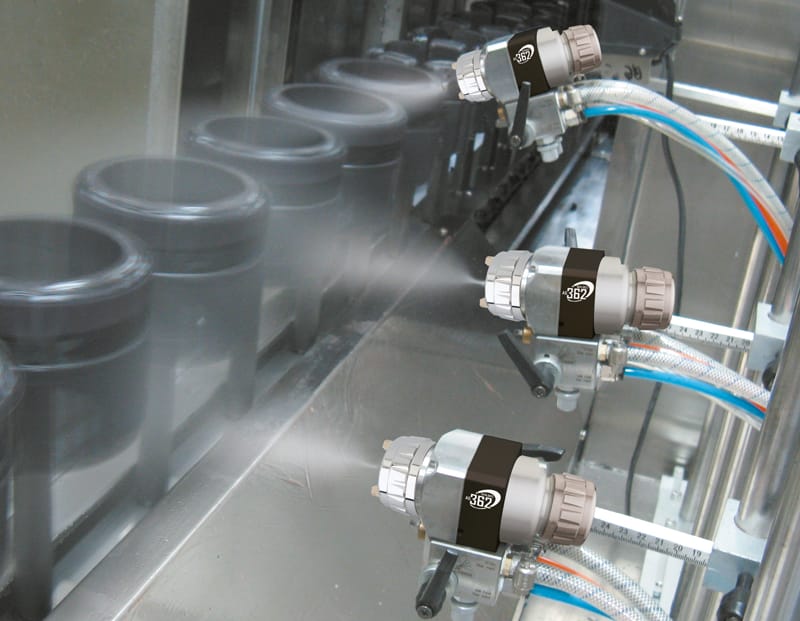
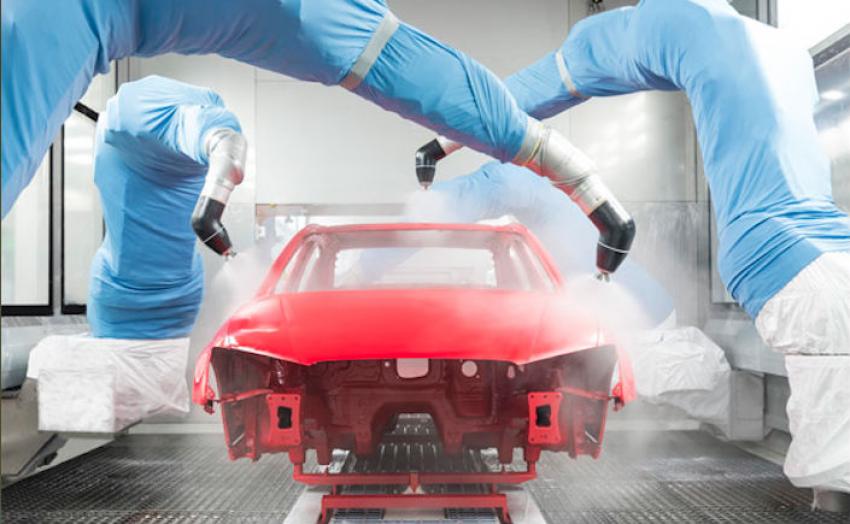
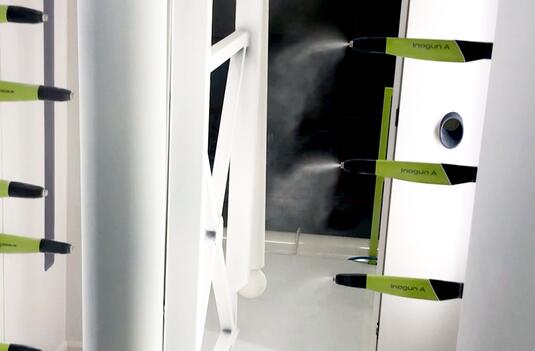

Material Handling System
- I Beam Conveyor.
- Power & Free Conveyors.
- Four Wheel conveyors.
- Closed Track /Clean Room Conveyors.
Types of Conveyors
As the name suggests, this family of conveyors are
installed on or below the floor level. Like overhead
conveyors, the floor conveyors basically comprise of chain,
track, drive unit, take up unit and oiler. Pegs / fixtures /
trolleys / pallets to support the component are generally
required depending on the type of component and
conveyor selected for the said application. The floor
conveyors are generally custom built depending on the
type of component to be handled as well as the
application / process requirement.
The word Overhead implies that these conveyors are installed
overhead, preferably just below the roof height. The conveyor is brought
down at lower levels only for loading / unloading purpose or for any
specific process requirement. An overhead conveyor basically consists of
a track, chain, drive unit, take up unit, oiler and carriers. The track is
supported from roof, floor, wall or columns as per site conditions. The
chain is guided in the track and moved by a drive unit. The take up unit is
provided to adjust the chain tension. The carriers are fixed to the chain at
a predefined pitch. The component to be conveyed is loaded on the
custom designed carrier. The oiler lubricates the chain. SFS has
experience of designing & installing long loops with multiple drive units
duly synchronized. SFS supplied conveyors to cater to unit loads up to
3000kgs.
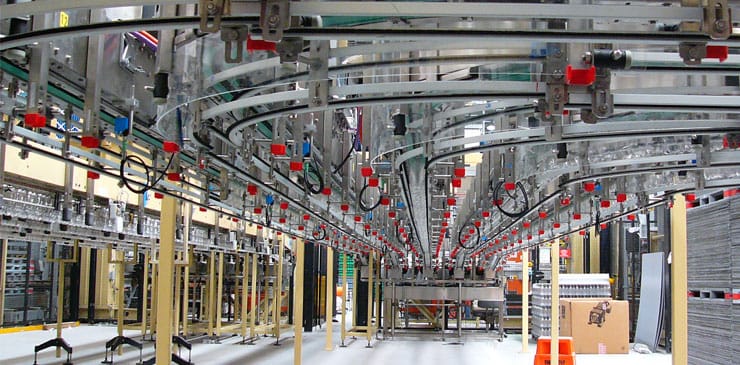
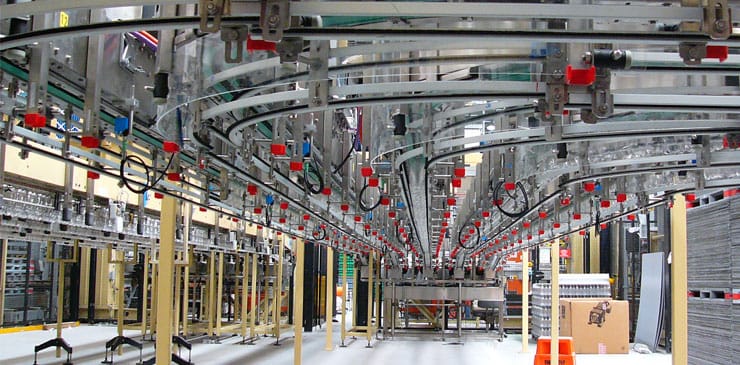
A hoist is a device used for lifting or lowering a load by means of a
drum or lift-wheel around which rope or chain wraps. It may be manually
operated, electrically or pneumatically driven and may use chain, fiber or
wire rope as its lifting medium. The most familiar form is an elevator, the
car of which is raised and lowered by a hoist mechanism. Most hoists
couple to their loads using a lifting hook.
Transporter
This is the main operational / Production equipment for loading and unloading jobs into various tanks in the chemical process, with a programmed cycle. It is effective replacement to traditional hoist with touch of automation. The cycle is based on timings required in particular tank, as specified, and also sequenced in such a way that critical tanks (degrease, de-rust, zinc phosphate and WDO) are treated on priority, so jobs will be removed from these tanks with minimal time loss (to avoid damage to job). To achieve this there an overhead motorized wagon, mounted on wheels which can travel across all tanks & load / unload stands. Further this wagon has an up / down arrangement, also motorized, for lifting & lowering jobs into tanks. The machine also has flight bar which can carry the loaded basket.
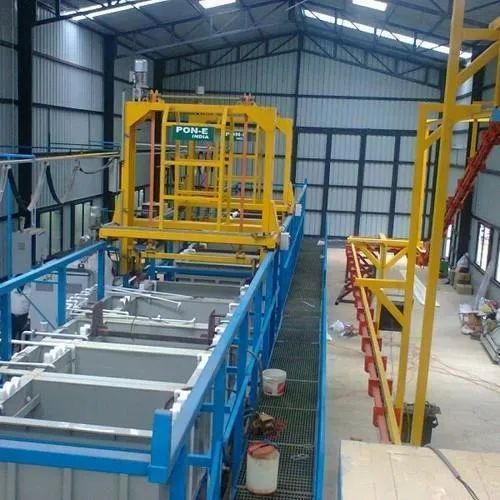
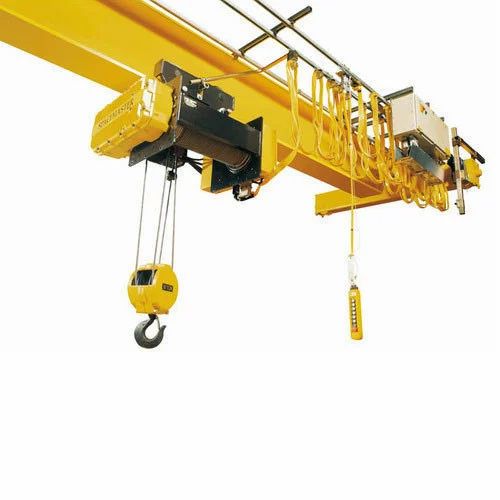
Transporter
This is the main operational / Production equipment for loading and unloading jobs into various tanks in the chemical process, with a programmed cycle. It is effective replacement to traditional hoist with touch of automation. The cycle is based on timings required in particular tank, as specified, and also sequenced in such a way that critical tanks (degrease, de-rust, zinc phosphate and WDO) are treated on priority, so jobs will be removed from these tanks with minimal time loss (to avoid damage to job). To achieve this there an overhead motorized wagon, mounted on wheels which can travel across all tanks & load / unload stands. Further this wagon has an up / down arrangement, also motorized, for lifting & lowering jobs into tanks. The machine also has flight bar which can carry the loaded basket.
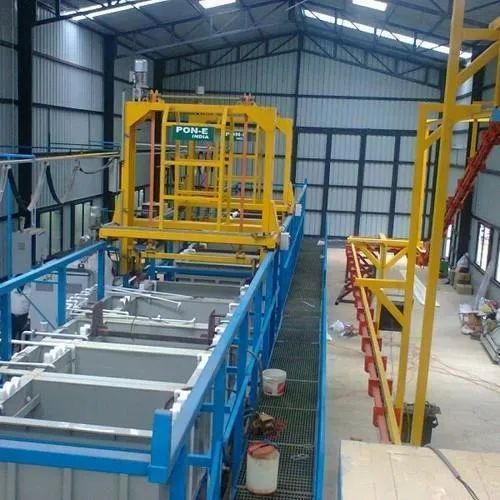
Air Supply System
An air handling unit(AHU) is the composition of elements mounted in large, accessible box-shaped units called modules, which house the appropriate ventilation requirements for purifying, air-conditioning or renewing the indoor air in a building or premises.
They are usually installed on the roof of buildings and, through ducts, the air is circulated to reach each of the rooms in the building in question.
Main functions of an AHU
In addition to managing the proper ventilation of the interior with outside air, the AHU performs other functions:
- Filtration and control of the quality of the air that will reach the interior, thanks to the air purification filters, and depending on the retention of these filters, the air will be clean.
- Control of the air temperature that regulates the air conditioning system in cold or hot, so that the thermal sensation in the interior is the desired one.
- Relative humidity monitoring for greater indoor comfort.
- Air intake: air handling units collect air from outside, which is treated and distributed throughout the rooms; and/or indoor air that is “recycled”.
- Filter: depending on the air purity requirements, the filter applied will have a higher or lower particle, viruses, bacteria, odours, and other air pollutants retention.
- Fan: this is an electromechanical system that powers the air to expel it from the AHU to the ducts that distribute the air throughout the rooms.
- Heat exchangers: devices that transfer temperature between two fluids, in this case, coolant and air, separated by a solid barrier.
- Cooling coil: the air passing through this module is cooled. In this process, water droplets can be generated, which are collected in a condensate tray thanks to the built-in droplet separator.
- Silencer: coatings that considerably reduce the sound level of the installation.
- Plenums: empty spaces in which the air flow is homogenised.
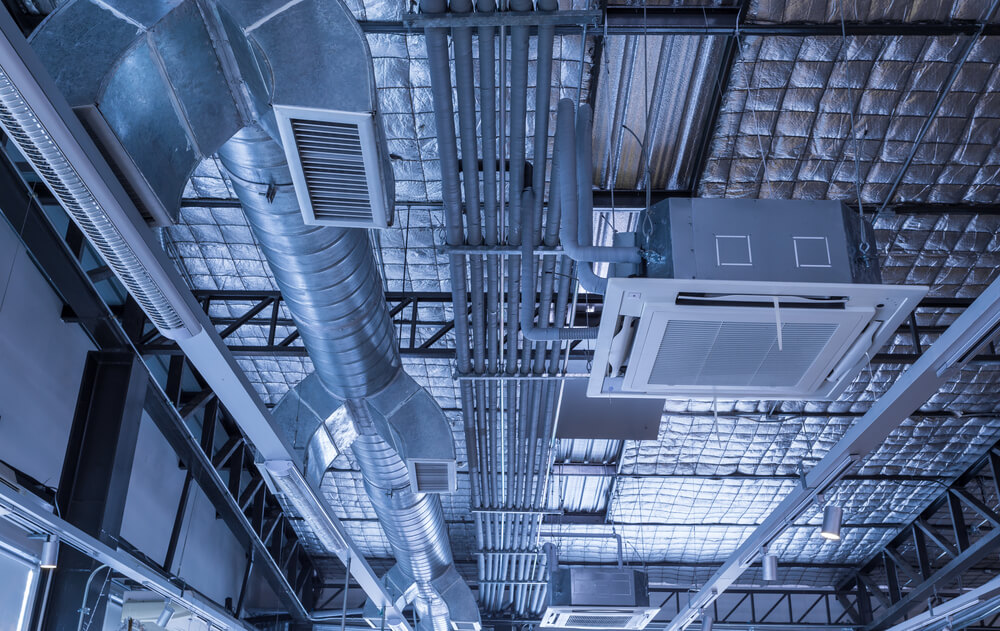
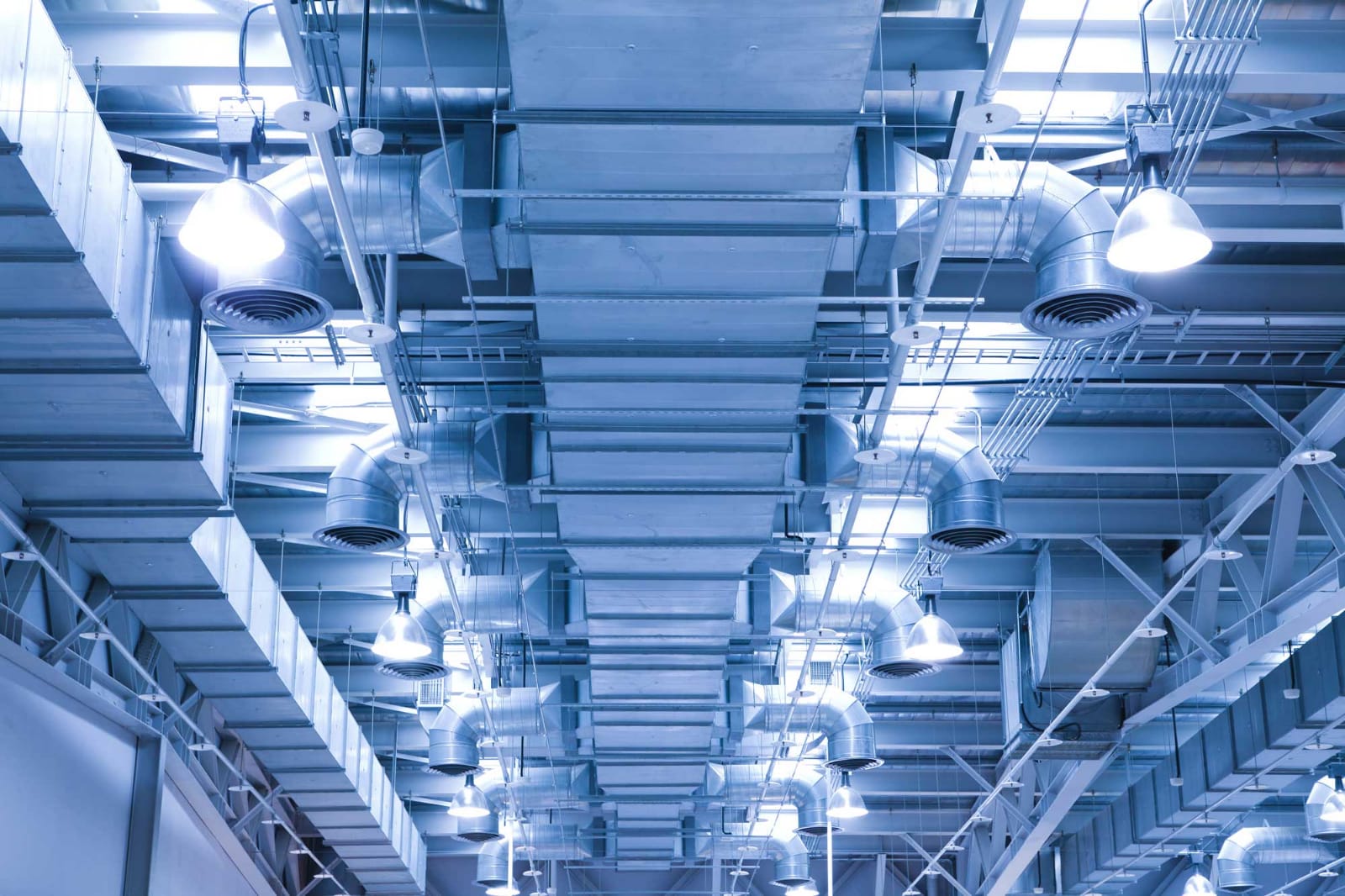
Shower tester booth
The primary motive of a why a shower tester booth is built is to make sure or test whether water will enter the particular vehicle or component and identify where the leaks are. Subsequently, the leakage areas have to be plugged. Every vehicle needs to be ensured that there is no leakage / seepage in rains. This shower tester booth uses high pressure nozzles where water hits the surface at high pressures to test whether water enters in or not. Water from the booth is also filtered and recycled.
SFS also supplies an air shower booth for quick drying of external surface to facilitate immediate inspection. The air shower booth consists of blowers that blow air at high velocity through air nozzles. In the air drying booth Special air knives are used to remove water and dry the surface quickly. Different programs can be tailor made to automate the entire process from opening of door to allow vehicle inside to roll out the vehicle out of the air shower booth. According to the clients requirement various levels of automation can be introduced.
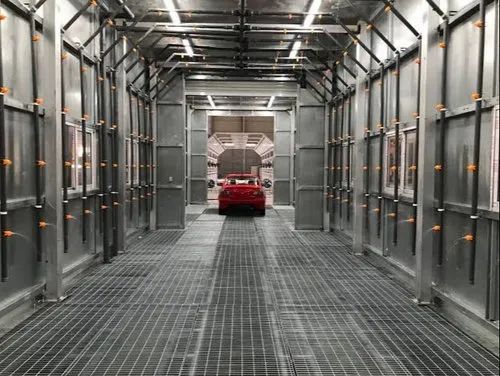
Cleanroom Enclosure Systems
Cleanroom enclosures built to the highest quality standard for todays critical environments. Modular cleanroom enclosures for every industry application. We supply all of the parts, labor and engineering needed to construct critical environment enclosure systems. Our services include initial design concept and on-site installation.
Modular cleanrooms are affordable, pre-fabricated enclosures. These cleanrooms offer a quality finish, professional look and can be custom built to meet the needs of the application. Modular cleanrooms can be integrated into current architecture and mechanical systems and generally do not disrupt current operations during installation.
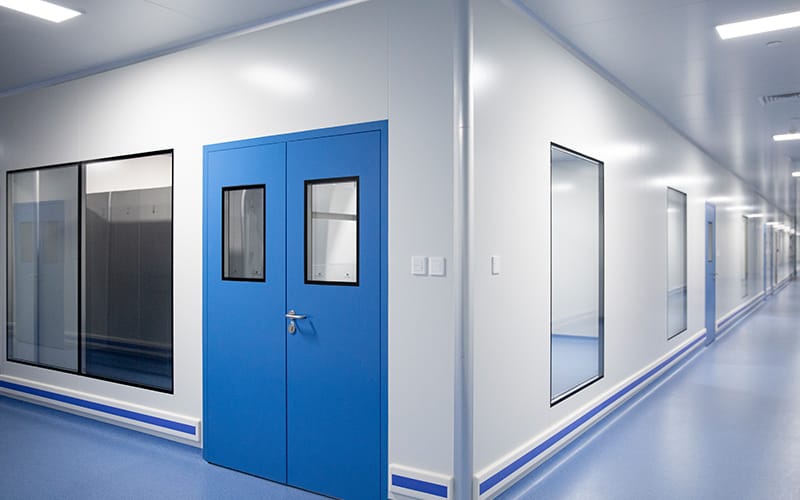
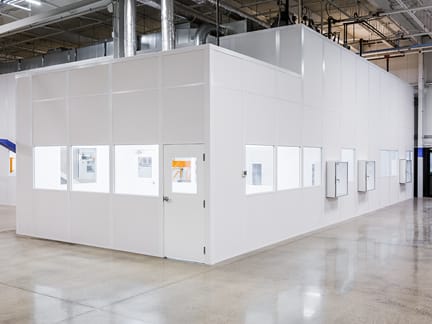